O laserowych sondach skanujących
Na podstawie danych pozyskanych w wyniku skanowania powstaje trójwymiarowy model powierzchni, który dzięki swojej dużej gęstości (często miliony punktów) zwany jest "chmurą punktów" lub "zbiorem punktów".
Kontakt

Skaner laserowy w kontekście metrologii przemysłowej może być wykorzystywany do kilku konkretnych celów. Wyposażone w oprogramowanie PC-DMIS i skanery laserowe ramię pomiarowe ROMER Absolute SI w sposób precyzyjny umożliwia realizację wszystkich tych zadań za pomocą jednego systemu. Enkodery Absolutne cały czas "wiedzą", gdzie znajduje się ramię (eliminując procedury zerowania), a dzięki ergonomicznej przeciwwadze ZeroG maszyna niemal "unosi się" w ręce operatora.
Na podstawie danych pozyskanych w wyniku skanowania powstaje trójwymiarowy model powierzchni, który dzięki swojej dużej gęstości (często miliony punktów) zwany jest "chmurą punktów" lub "zbiorem punktów". Zobacz pojazd jako dużą chmurę punktów. Różne kolory odzwierciedlają poszczególne płaszczyzny skanowania części.
Kontrola Obiektu i Weryfikacja
Chmura punktów 3D stworzona za pomocą ramienia pomiarowego ROMER Absolute SI o 7 osiach współziałającego z oprogramowaniem PC-DMIS może być wykorzystywana do kontroli wymiarowej bądź GD&T (tolerancja kształtu i położenia), a wyniki porównywane względem nominalnych wartości CAD. Dzięki porównaniu chmury punktów z CAD (Cloud-to-CAD), duże chmury punktów mogą zostać nałożone na model CAD, co umożliwia szybką wizualną kontrolę odchyłek (czasami zwaną "statystyczną mapą odchyłek" bądź "kolorową mapą odchyłek"). Skaner laserowy może być również wykorzystywany do tradycyjnych (nie przeprowadzanych na podstawie modelu CAD) pomiarów konstrukcji cech oraz wymiarowania.
Przykłady kontroli i weryfikacji:
• Weryfikacja typu "część względem modelu CAD" dla kontroli początkowej, kontroli w trakcie trwania procesu produkcji oraz weryfikacji ostatecznej
• Weryfikacja wymiarów narzędzi i matryc, aby określić zużycie, dokonać oceny naprawy lub kontroli modyfikacji
• Kontrola pierwszego produktu
• Pomiar konturów, porównanie części z odpowiadającymi im modelami CAD, przekroje 2D lub mapy topograficzne 3D
• Odpowiednie dopasowanie linii produkcyjnej lub procesów montażowych
• Kontrola dopasowania dwóch elementów.
Inżynieria Odwrotna
Inżynieria odwrotna to proces, w którym na podstawie obiektu faktycznego, poprzez jego pomiar mający na celu określenie jego właściwości technicznych, otrzymujemy model CAD. Często inżynieria odwrotna jest przeprowadzana, gdy proces projektowania produktu wymaga czynności manualnych, tak jak podczas konstrukcji pojazdu. Mimo rozwoju CAD, wiele projektów rozpoczyna swoje życie jak model rzeczywisty, który następnie musi zostać przekształcony w model cyfrowy.
Wygenerowane przez skaner laserowy chmury punktów są obrabiane i przetwarzane na wiele sposobów, by przygotować je do konwersji do modelu CAD. Programy do inżynierii odwrotnej, takie jak PC-DMIS Reshaper, wykorzystywane są do generowania lub importowania zeskanowanej chmury punktów, przetwarzania, matematycznego wygładzania i łączenia zeskanowanych danych tak, aby stworzyć reprezentatywny model powierzchni.
Przykłady zastosowania inżynierii wstecznej:
• Tworzenie modeli 3D do dalszego projektowania i przystosowania
• Ocena współpracujących powierzchni w celu połączenia lub dołączenia innej części
• Odtwarzanie dokumentacji części "zabytkowych" lub "złotych", dla których nie istnieje model CAD bądź rysunki
• Tworzenie modeli "powykonawczych" (rzeczywistych) narzędzi, aby sprawdzić ich zużycie
• Analiza konkurencyjnej części/produktu
• Ochrona obiektów archiwalnych lub historycznych poprzez tworzenie zapisu 3D lub kopii
Kopia/Skalowalność/Frezowanie i Szybkie Prototypownie
Jednorazowe repliki nie wymagają stworzenia pełnego modelu CAD. W wielu przypadkach modele stereolitograficzne lub frezowanie oparte na CAM mogą zostać zrealizowane bezpośrednio w oparciu o dane pomiarowe w postaci chmury punktów lub modelu Mesh (siatka trójkątów). Możliwa jest także prosta zmiana rozmiaru lub skalowanie modelu. Oprogramowanie CAM wykorzystywane jest do odczytu uzyskanych danych w postaci chmur punktów oraz opracowania instrukcji obróbki na maszynach CNC.
Przykładowe zastosowania:
• Ochrona dziedzictwa kulturowego i obiektów historycznych, gdzie przeprowadza się skanowanie obiektów, aby obserwować ich zniszczenie lub zużycie
• Szybkie prototypownie ręcznie utworzonych modeli
• Przeskalowanie skanowanych modeli rzeczywistych
• Skanowanie modeli do celów elektronicznych, takich jak filmy i gry wideo
Jak szybie jest skanowanie?
Szybkość skanowania w znacznej mierze zależy od sondy i jej pola widzenia. W przypadku sond laserowych punkty zebrane "na ekranie" można obserwować w czasie rzeczywistym. Czasami proces ten nazywany jest "malowaniem części". Zapewniające ustawienie odpowiedniej geometrii skanowanie pod różnymi kątami często skutkuje wygenerowaniem chmury punktów, takiej jak w przypadku Liberty Bell (Dzwon Wolności) przedstawionej na rysunku 3, która wygląda jakby ktoś szalał z farbą w ręce.
Ogółem dla szybkości skanowania duże znacznie ma również ilość pobieranych punktów na sekundę oraz szerokość ścieżki skanowania i gęstość punktów w linii skanowania. Poniższa animacja przedstawia różnice między dwoma skanerami - jednym z wąską i drugim z szeroką linią (wiązką) lasera, mierzącymi 1 metr kwadratowy płaskiej powierzchni w centralnej części pola widzenia. Skaner z szerszą wiązką lasera (105 mm) w centralnej części pola widzenia mierzy powierzchnię w mniej niż 3 minuty, natomiast skanerowi z węższą wiązką lasera pomiar tej samej części zajmuje ponad 13 minut.
Bardzo ważne w wyborze skanera jest zadanie pomiarowe, które chcemy zrealizować. Pomiary, w których znaczenie mają nie drobne szczegóły, ale szybkość i zasięg lasera, wymagają zastosowania szybszych skanerów. W przypadku mniejszych, bardziej złożonych części skanowanie może przebiegać sprawniej przy zastosowaniu lasera z węższą wiązką. Niektóre skanery, takie jak HP-L-20.8, umożliwiają użytkownikowi wybór szerokości pasma lasera najlepszego do realizacji jego zadań pomiarowych.
Skaner z wąską wiązką laserową | Skaner z szeroką wiązką laserową |
44 mm szerokość linii w centrum pola widzenia | 105 mm szerokość linii w centrum pola widzenia |
23 wykonane ruchy dla całej powierzchni | 10 wykonanych ruchów dla całej powierzchni |
1 mm odległość między liniami, 13 minut, 2 sekundy | 1 mm odległość między liniami, 2 minuty, 50 sekund |
Czy większa ilość punktów jest lepsza?
To zależy od rodzaju skanowanej części. W przypadku złożonych powierzchni z licznymi krzywymi skaner o większej gęstości optycznej stanowi znacznie lepsze rozwiązanie. Jednak dla bardziej płaskich powierzchni już nie. Pozyskiwanie charakterystyk takich elementów jak otwory, szczeliny, elementy walcowe i inne pryzmatyczne kształty oraz krawędzie znacznie lepiej przebiega przy zastosowaniu danych o większej gęstości. Proszę porównać dwie niżej przedstawione ilustracje - to skany identycznego 15 mm otworu. Obraz po lewej powstał przy zastosowaniu sondy skanującej o niskiej gęstości optycznej skanera. Natomiast skan po prawej został wykonany za pomocą unikatowej sondy V5. Pomiar kształtu otworu znajdującego się po prawej stronie okazał się bardziej precyzyjny przy wykorzystaniu danych o większej gęstości. Dane te umożliwiają także efektywną kontrolę tekstury obiektu.
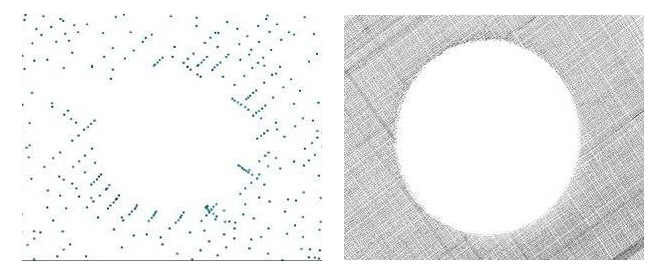
Czy światło otoczenia ma wpływ na sondę?
W wielu przypadkach oświetlenie występujące w laboratorium, studio oraz w środowisku przemysłowym może mieć negatywny wpływ na urządzenie optyczne. Wiele rodzajów skanerów musi pracować przy odpowiednio kontrolowanym świetle. Nie dotyczy to sond ramion pomiarowych ROMER Absolute Arms. Te wyposażone w skanery laserowe ramiona wykorzystują różnorodne techniki, aby zniwelować skutki światła otoczenia, w tym filtry optyczne oraz kontrolę narażenia (ekspozycji), która została zaprojektowana w taki sposób, aby ignorować długości fal świetlnych, oprócz tych znajdujących się w pobliżu działającego lasera. Efekt netto jest taki, że światło z lampy rtęciowej, żarowej lub halogenowej bądź też innych popularnych systemów oświetleniowych jest odrzucane, a tym samym nie oddziałuje na sondę.
Czy rodzaj powierzchni wpływa na działanie sensora laserowego?
Dawniej dokładność pomiarowa zależała od wykończenia powierzchni mierzonych elementów. Mocno polerowane chromowe i błyszczące, czarne powierzchnie były najtrudniejsze do skanowania. Wielokolorowe powierzchnie lub powierzchnie z wysokim współczynnikiem odbicia również stanowiły problem dla wielu skanerów. Ramię pomiarowe ROMER Absolute Arm posiada wiele narzędzi, które umożliwiają efektywne skanowanie większości wykończeń powierzchni oraz powierzchni różnokolorowych. Nasz skaner laserowy HP-L-20.8 posiada funkcję automatycznej kontroli ekspozycji na światło oraz unikatową technologię „flying dot", dzięki którym automatycznie i w czasie rzeczywistym dopasowuje się do zmian koloru materiału i współczynnika odbicia, co umożliwia mu skanowanie niemal każdego rodzaju powierzchni. Po prawej stronie na ilustracji widzimy element w trzech różnych kolorach, z różnymi wykończeniami powierzchni oraz o różnorodnym współczynniku odbicia, który bez problemu mierzony jest przez skaner HP-L-20.8.
Czy muszę stosować proszek?
W przypadku wszystkich powierzchni, z wyjątkiem tych najbardziej przezroczystych, odpowiedzieć brzmi: "NIE". Przygotowanie powierzchni poprzez rozpylenie proszku (aby zmniejszyć współczynnik odbicia i ujednolicić powierzchnię) jest wręcz niepożądane i to z wielu powodów - m.in. dlatego, że proces przygotowania powierzchni jest czasochłonny, a wyniki pomiarowe mogą być zmienne wskutek zastosowania proszku (wg badań taka zmienność może wynieść nawet 100 mikronów/.004"). Dawniej bardzo często stosowano proszek. Dziś już się tego nie praktykuje.
Czy temperatura i środowisko mają wpływ na sondę?
Typowe środowisko produkcyjne jest jak najbardziej odpowiednie dla ramion pomiarowych ROMER Absolute Arm ze skanerami laserowymi. Sondy nie nadają się do pracy w środowisku, w którym są bezpośrednio narażone na kontakt z wodą lub olejem, ponieważ wpływa to niekorzystnie na laser i obiektyw kamery. Standardowo temperatura powinna mieścić się w przedziale od 15 do 35 stopni Celsjusza, a wilgotność powietrza w zakresie od 0 do 90% bez kondensacji. Należy unikać środowiska, w którym obecny jest brud, olej i inne zanieczyszczenia oddziałujące na sondę, co może mieć wpływ na dokładność pomiarową. Sondy te mogą być stosowane w środowisku przemysłowym przez wiele lat, 24 godziny na dobę/7 dni w tygodniu. Nie obniży to ich wiarygodności pomiarowej.
Przefiltrowane czy nieprzefiltrowane dane ... Jaka jest faktyczna różnica?
Przefiltrowane dane to dane sondy, które zostały "przefiltrowane" lub "przetworzone" podczas generowania chmury punktów. Zazwyczaj proces ten jest przeprowadzany przez pakiet oprogramowania innego producenta, gdy dane sondy są odczytywane w programie. "Surowe" dane sondy stanowią pewnego rodzaju niewiadomą, jako że są filtrowane "podczas pozyskiwania", dlatego ich jakość może być niska.
Dane nieprzefiltrowane to dane sondy w stanie surowym, w tym - niezależnie od przyczyny - wszystkie dane odstające. Oryginalne dane mogą zostać oszacowane w sposób niezależny od strony trzeciej. Wykorzystując dane nieprzefiltrowane otrzymujemy prawdziwy obraz dokładności pomiarowej sondy i możemy porównać rzeczywiste dane z nominalnymi (druk lub CAD).
Możliwość pozyskania "surowych", nieprzefiltrowanych danych niezależnie od jakiegokolwiek oprogramowania innego producenta to ogromna zaleta, ponieważ pozwala nam wybrać te informacje, które chcemy umieścić w naszym zestawie danych. Często dane odstające są rezultatem niskiej wydajności skanera. Dlatego im skaner dokonuje lepszych pomiarów rzeczywistej powierzchni i nie jest "oszałamiany" przez zewnętrzne czynniki, takie jak oświetlenie, kolor i odbicie powierzchni, tym bardziej wiarygodne wyniki otrzymujemy. Większość programów do tworzenia chmur punktów bądź kontroli posiada narzędzia umożliwiające ignorowanie lub usunięcie, wedle naszego uznania, danych odstających.
Czy po zakończeniu skanowania otrzymam model CAD?
To prawdopodobnie największe nieporozumienie związane ze skanerami laserowymi. Ramię pomiarowe i skaner badają geometrię części, generując chmury punktów 3D. Chmura punktów to zbiór wielu milionów punktów stanowiący sam w sobie dokładny model 3D skanowanego obiektu. Nie jest jednak modelem CAD. Aby uzyskać model CAD, chmury punktów muszą zostać poddane obróbce. Najpierw trzeba stworzyć rodzaj modelu opartego na siatce poligonów. W istocie chodzi więc o to, żeby duży zbiór punktów przekształcić w zbiór połączonych ze sobą powierzchni wyrażonych poprzez trójkąty lub wieloboki i tym samym uzyskać nowy model 3D, który będzie zamkniętym wielościanem. Kolejnym krokiem jest weryfikacja i analiza powierzchni oraz cech do stworzenia modelu CAD, często w systemie CAD. Procesy te można przeprowadzić w trybie offline po zakończeniu pozyskiwania danych skanowania. To najbardziej czasochłonny etap pracy z danymi skanowania 3D. Zdjęcie po lewej przedstawia chmurę punktów, na której różnorodne obszary skanowania zaznaczono jako wielokolorowe łatki. Po prawej te same dane zostały przekształcone w model oparty na siatce poligonów. To dopiero pierwszy etap w procesie obróbki i przekształcania chmur punktów w model CAD.
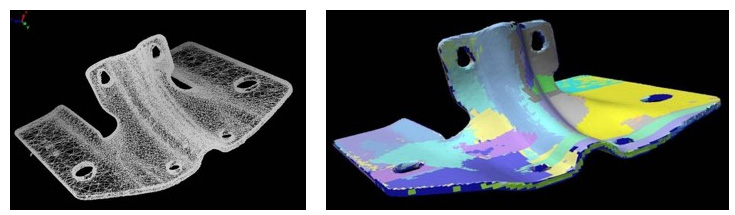