Laserscanners
De uitvoer van een laserscanner is een driedimensionaal model van een oppervlak, dat vanwege de hoge dichtheid (vaak miljoenen punten) een 'puntenwolk' genoemd wordt.
Contact opnemen

Laserscans kunnen in het kader van industriële metrologie gebruikt worden voor een aantal duidelijke doeleinden. ROMER SI Absolute Arms met zeven assen zijn uitgerust met PC-DMIS-software en 3D laserscanners en voeren al deze functies uit in één systeem. De Absolute Encoders 'weten' altijd waar de arm is (waarmee terugkeren naar referentiepositie overbodig is) en het ergonomische zero-G-tegengewicht laten hem haast zweven in de hand van de bediener.
De uitvoer van een laserscanner is een driedimensionaal model van een oppervlak, dat vanwege de hoge dichtheid (vaak miljoenen punten) een 'puntenwolk' genoemd wordt. Geeft een grote puntenwolk weer die een volledig voertuig voorstelt. De verschillende kleuren staan voor de verschillende afzonderlijke scans van het onderdeel.
Doelinspectie en validatie
De 3D puntenwolk die gemaakt is met de 7-assige Absolute Arm in combinatie met PC-DMIS kan worden gebruikt voor dimensionele inspectie of controle van vorm- en plaatstoleranties en de resultaten kunnen worden vergeleken met nominale CAD-waarden. Met de vergelijking van wolk en CAD kunnen grote puntenwolken als overlay weergegeven worden voor een snelle visuele inspectie van afwijkingen. Laserscans kunnen ook worden gebruikt voor traditionele inspectie (zonder CAD) met het construeren en meten van kenmerken.
Voorbeeld inspectie- en validatietoepassingen:
- Verifiëren of een onderdeel overeenkomt met het CAD model, voor inspectie bij ontvangst, inspectie tijdens het proces of uiteindelijke validatie.
- Verifieer gereedschapafmetingen om slijtage te bepalen, reparaties te evalueren of aanpassingen te controleren
- Inspectie van eerste product
- Contourmeting, onderdelen vergelijken met bijbehorende CAD-modellen, 2D dwarsdoorsnede of 3D topografisch karteren
- Nauwkeurig afstemmen van productielijn of assemblageproces Inspectie van twee in elkaar passende onderdelen
Reverse-engineering
Reverse-engineering is het proces waarbij een fysiek onderdeel gemeten wordt om de karakteristieken ervan te bepalen en de data verwerkt worden om een CAD-model te maken. Dit wordt vaak gedaan in gevallen waarbij het productontwerp significante handmatige bewerkingen kent, zoals auto-ontwerp. Ondanks de voordelen van CAD beginnen veel ontwerpen nog steeds als fysiek model dat vervolgens in digitale vorm moet worden gegoten.
Puntenwolken gegenereerd met laserscans worden op verschillende manieren verwerkt om ze klaar te maken voor omzetting naar CAD. Software voor reverse-engineering, zoals PC-DMIS Reshaper wordt gebruikt om de gescande puntenwolk te maken of te importeren, om de gescande data te manipuleren, wiskundig te effenen en te combineren zodat een representatief oppervlaktemodel gemaakt kan worden.
Toepassingen van reverse-engineering:
- Een 3D model maken voor verder ontwerp of verder aanpassing in CAD
- Karakterisering van een passend oppervlak zodat een ander stuk eraan verbonden of vastgemaakt kan worden
- Een "origineel" of "gouden" onderdeel creëren waar geen CAD- of onderdelentekening van bestaat
- Een "as-built"-model van een gereedschap maken om slijtage na verloop van tijd mee te vergelijken
- Analyse van concurrerende onderdelen/producten
- Archiveren of behouden van historische voorwerpen om een 3D record of kopie te maken
Kopie/schaalmodel frezen en snelle prototypes
Voor eenmalige replica's is het mogelijk niet nodig om een volledig CAD-model te maken. Modellen maken met stereolithografie of frezen op basis van CAM kan in veel gevallen direct met de scandata van de puntenwolk of het roostermodel gedaan worden. Het formaat of de schaal aanpassen kan op basisniveau mogelijk zijn. CAM-software wordt gebruikt om de scandata te lezen en de machine-instructies te produceren voor CNC-machinegereedschap.
Toepassingen:
- Conservatie van historisch of cultureel erfgoed waarbij voorwerpen gescand worden om slijtage of beschadiging te observeren
- Snelle prototypes maken van handgemaakte modellen
- De schaal aanpassen van een fysiek gescand model
- Modellen scannen voor elektronische doeleinden zoals films en videospellen
Hoe snel gaat het scannen?
De scansnelheid hangt significant af van de taster en het gezichtsveld van de taster. Met lasertasters kunt u in het algemeen de verzamelde punten in real-time op het scherm zien. Dit wordt soms wel "het onderdeel schilderen" genoemd. Scans uitvoeren vanuit verschillende hoeken om te zorgen dat alle relevante geometrie opgenomen wordt, resulteert vaak in een puntenwolk zoals die van de Liberty Bell in afbeelding 3, die eruitziet alsof iemand erop los is gegaan met een verfspuit.
Wat ook belangrijk is voor de algehele snelheid zijn het aantal punten per seconde dat de scanner kan verwerken, de breedte van het scanpad, en de puntdichtheid per lijn. De onderstaande animatie vergelijkt het verschil tussen twee scanners, één met een smalle streep en één met een brede streep, waarmee een vlakke plaat van 1 vierkante meter opgenomen wordt met een gezichtsveld in het midden. De scanner met een bredere lijnbreedte (105 mm) met een gezichtsveld in het midden, neemt het oppervlak op in een kleine 3 minuten, terwijl de scanner met de smallere lijnbreedte 13 minuten over hetzelfde onderdeel zou doen.
De toepassing kan een factor zijn bij de keuze voor een scanner. Toepassingen waarbij snelheid en dekking uiterst belangrijk zijn, maar kleine details niet, kunnen vragen om een scanner met hogere snelheid. Andere toepassingen met kleinere, complexere onderdelen gaan mogelijk beter met een kleinere streepbreedte. Op sommige scanners, zoals de HP-L-20.8 kunnen gebruikers een streepbreedte selecteren die het beste bij de toepassing past.
Scanner met smalle scanbreedte | Scanner met brede scanbreedte |
Lijn van 44 mm met gezichtsveld in het midden | Lijn van 105 mm met gezichtsveld in het midden |
23 scans om plaat te "schilderen" | 10 scans om plaat te "schilderen" |
Lijnafstand van 1 mm, 13 min, 2 sec | Lijnafstand van 1 mm, 2 min 50 sec |
Zijn meer punten beter?
Dat is deels afhankelijk van waarvoor u de data wilt gebruiken. Oppervlakken die zeer complex zijn met veel rondingen zijn gebaat bij scannen met een hogere dichtheid. Voor vlakkere oppervlakken geldt dat minder. Het extraheren van karakteristieken zoals gaten, sleuven, cilinders en andere prismatische vormen, en van randen zal ook gebaat zijn bij data met hogere dichtheid. Bekijk de twee onderstaande afbeeldingen eens, beide scans van een gat van 15 mm. De scan links is gemaakt met een scantaster met lage dichtheid, de scan rechts met de eersteklas V5-taster. De extractie en meting van de vorm van het gat rechts zal nauwkeuriger zijn met de hogere dichtheid aan data. Met een hogere dichtheid dat zullen texturen ook beter vastgelegd worden, mocht dat belangrijk zijn.
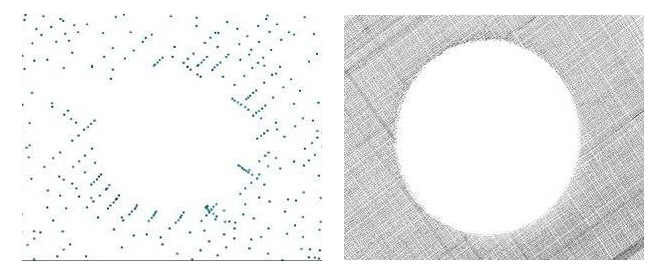
Heeft omgevingslicht invloed op de sensor?
In veel gevallen kan verlichting in een laboratorium, studio en fabriek een nadelig effect hebben op een optisch apparaat. Hoewel voor sommige scantoestellen een omgeving met gecontroleerd licht nodig is, geldt dat niet voor tasters die op ROMER-armen gebruikt worden. ROMER-armen met laserscanners gebruiken verscheidene technieken om de effecten van omgevingslicht te ondervangen, zoals optische filters en belichtingscontroles die ontworpen zijn om de golflengten van licht te negeren behalve die van de gebruikte laser. Het effect is dat licht van gloeilampen, kwikdamp, halogeen en andere populaire verlichtingen genegeerd worden en niet van invloed zijn op de sensor.
Is de toestand van het oppervlak van invloed op de sensor?
Voorheen werd de nauwkeurigheid van metingen beïnvloed door de afwerking van oppervlakken. hooggepolijste chromen en glanzende zwarte oppervlakken waren het moeilijkst om te scannen. Meerkleurige oppervlakken of oppervlakken met een overgang in reflectiviteit kunnen voor veel scanners ook problemen veroorzaken. ROMER-armen met laserscanners gebruiken gereedschappen om met deze situaties om te gaan, waardoor de meeste afwerkingen en kleuren van oppervlakken goed gescand kunnen worden. Onze eersteklas HP-L-20.8-sensor gebruikt automatische belichtingscontrole en Flying Dot-technologie om zich automatisch en in real-time aan te passen aan veranderingen in de kleur en reflectiviteit van materialen, waardoor het gemakkelijk is om vrijwel alles met succes te scannen. In de afbeelding aan de rechterkant is een onderdeel met drie verschillende kleuren en afwerkingen, en variërende reflectiviteit gemakkelijk gescand met de HP-L-20.8.
Moeten de onderdelen gepoederd worden?
Het antwoord is nee voor alle oppervlakken behalve bij hoge transparantie. Voorbereiding van het oppervlak door het te behandelen met een poeder (om reflectiviteit te beperken en een uniform oppervlak te creëren) is om verschillende redenen ongewenst, te beginnen bij de extra tijd die de voorbereiding van het oppervlak kost tot de variatie in metingen door het poeder zelf (uit onderzoek blijkt dat dit wel 100 microns kan zijn). Hoewel het vroeger vaak zo was dat onderdelen gepoederd moesten worden, tegenwoordig is dat niet meer het geval.
Zijn temperatuur en omgeving van invloed op de sensor?
Typische fabrieks- en werkplaatsomgevingen zijn aanvaardbaar voor de werking van ROMER-armen met laserscanners. De sensoren zijn niet geschikt voor gebruik in omgevingen waar water of olie gespoten wordt omdat deze vloeistoffen zich aan de laser en cameralenzen kunnen hechten. De temperatuur moet normaal gesproken tussen de 15 en 35 °C liggen en de luchtvochtigheid tussen de 0 en 90% niet-condenserend. Omgevingen waar vuil, olie of andere verontreinigingen aanwezig zijn die zich kunnen hechten aan de sensor moeten worden vermeden, dit kan de prestaties van metingen beïnvloeden. Deze sensoren kunnen jarenlang 24 uur per dag betrouwbaar werken in fabrieksomgevingen.
Gefilterde en ongefilterde data... Wat is nu eigenlijk het verschil?
Gefilterde data zijn sensordata die "gefilterd" of "verwerkt" zijn terwijl de puntenwolk gegenereerd wordt. Dit wordt meestal gedaan door softwarepakketten van andere fabrikanten terwijl de sensordata in de software ingelezen worden. De ruwe sensordata komen in gevaar omdat ze gefilterd worden tijdens de opname, waardoor datakwaliteit een onbekende factor is.
Ongefilterde data zijn sensordata in de ruwe vorm, inclusief alle uitschieters, ongeacht de oorzaak. De oorspronkelijke data kunnen onafhankelijk worden geëvalueerd. Het gebruik van ongefilterde data biedt de ware capaciteit van de mogelijkheid van de sensoren om nauwkeurig te meten, om ware data te vergelijken met nominale data (print of CAD).
De mogelijkheid om ruwe, ongefilterde scandata vast te leggen los van software van derden verdient de voorkeur, gewoon omdat het u in staat stelt om te bepalen wat wel niet opgenomen wordt in uw dataset. Vaak worden uitschieters in data veroorzaakt door slechte prestaties van de scanner, dus hoe beter uw scanner in staat is om het ware oppervlak vast te leggen en niet "voor de gek gehouden wordt" door externe factoren zoals belichting, kleur en reflectiviteit van het oppervlak, hoe meer u kunt vertrouwen op de resultaten. De meeste puntenwolkpakketten of inspectiepakketten hebben hulpmiddelen om uitschieters naar wens te verwijderen of te negeren.
Krijg ik na afloop van het scannen van een onderdeel een CAD-model?
Dit is misschien wel het aspect van laserscannen dat het vaakst verkeerd wordt begrepen. De arm en scanner leggen de geometrie van het onderdeel vast in een puntenwolk in 3D. Dit is slechts een bestand met de punten in verhouding tot elkaar, het is geen CAD-bestand. Voor een CAD-bestand moet u eerst een soort polygoon model maken van de puntenwolken, en vervolgens de oppervlakken en kenmerken karakteriseren als CAD-model, meestal in een CAD-systeem. Dit zijn offline processen die gebeuren wanneer de scandataverzameling voltooid is, en is feitelijk het meest tijdrovende deel van het werken met de 3D scandata. De afbeelding aan de linkerkant is een puntenwolk met wederom de verschillende gescande delen als verschillend gekleurde stukken, het model aan de rechterkant is dezelfde data geconverteerd naar een polygonaal model, pas de eerste stap naar een volledige CAD-conversie.
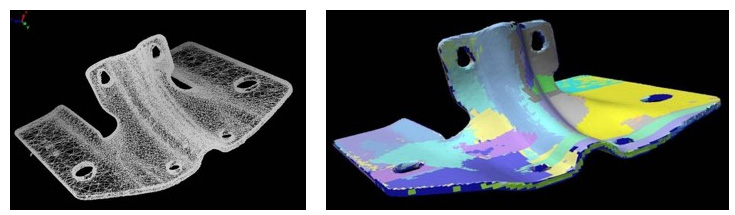