Effizienter und zeitsparender, mit höherer Erfolgsgarantie
Modernes Streifenlichtscanning für neue Standards im Qualitätsmanagement für Lifestyle-Güter.
Kontakt
Seit mehr als 270 Jahren steht der Name Villeroy & Boch für hochwertige Keramikprodukte aus den Bereichen Bad und Wellness sowie Dining & Lifestyle. Das 1748 gegründete Unternehmen hat seinen Hauptsitz in einer alten Abtei in Mettlach, Deutschland, und besitzt 13 Produktionsstätten in Europa und Asien. Rund 7.100 Mitarbeiter:innen betreuen die Produktion, Vermarktung und den Verkauf hochwertiger Keramikwaren vom klassischen Tischservice und Produkten für den Sanitärbereich bis hin zu Armaturen, Möbeln und Dekorationsartikeln.
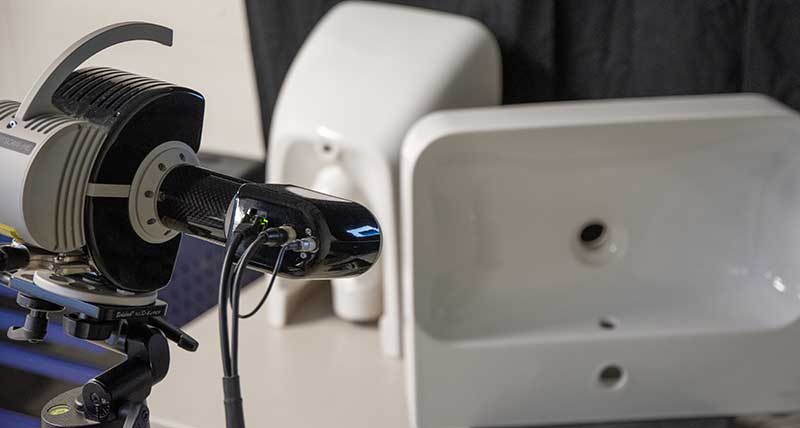
Als ein Baustein des internen Projektes „Digitale Validierung“, erwarb Villeroy & Boch Ende 2018 den Hexagon-Streifenlichtscanner SmartScan. „Die meisten 3D-Scanner benötigen Messmarken, um die einzelnen Scans zueinander zu referenzieren. Das Anbringen und das anschließende Entfernen der Marken sind sehr zeitaufwendig. Beim SmartScan ist das nicht nötig“, erläutert Miguel Ramalhosa aus dem Total Quality Management bei Villeroy & Boch in Mettlach die Entscheidung. „Zudem ist der Drehteller zum automatisierten Scannen der Bauteile eine gute Sache. Weitere ausschlaggebende Punkte waren die Mobilität und die Schnelligkeit des SmartScan-Systems.“
Digitale Validierung
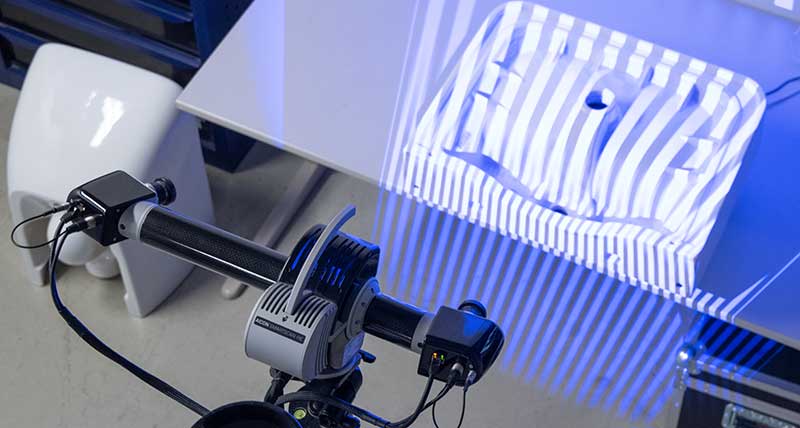
Um die rund 50 Maße, die jede Checkliste enthält, zu überprüfen, werden im Laufe der Validierung immer wieder Messreihen mit den neuen Produkten durchgeführt. Dafür werden die zu inspizierenden Bauteile auf einem Drehteller platziert und mit dem SmartScan automatisiert gescannt. Mit einem aus den Scans erstellten STL-Modell werden im Anschluss in der Inspektionssoftware PolyWorks die voreingestellten Checklisten-Maße abgeglichen. Liegen alle Maße innerhalb der Toleranz und entspricht das Produkt allen Sollvorgaben, ist die Produktion dieses Bauteils validiert.
In der digitalen Welt ist ganz klar festgelegt, wo das Maß abgenommen werden muss. Das sehe ich als großen Vorteil.Vor Anschaffung des SmartScans musste diese Aufgabe noch komplett händisch mit Lineal, Zirkel, Innentaster und Winkel erledigt werden. Die so abgenommenen Maße wurden dann mit der Hand auf einer ausgedruckten Checkliste eingetragen. Doch gerade bei komplizierten oder sehr sanft geformten Bauteilen ist ein genaues Handaufmaß gar nicht möglich.
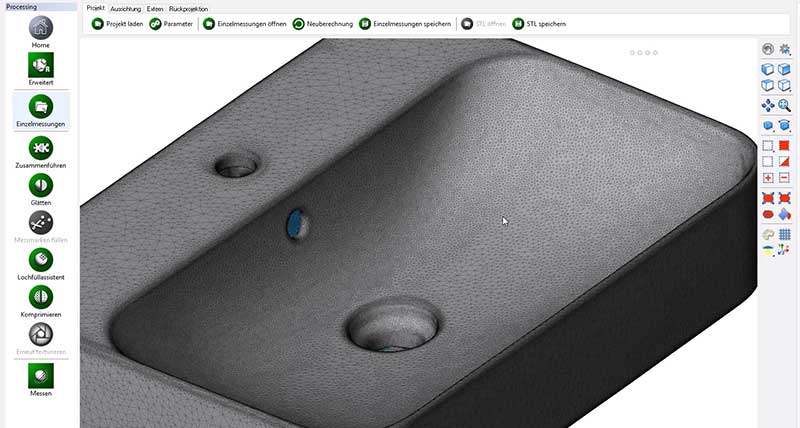
Auch bei der Behebung von auftretenden Problemen sieht Miguel Ramalhosa großes Potential für den Einsatz vom Streifenlichtscanning: „Gerade bei Modellen, bei denen es zum Beispiel darauf ankommt, dass die Zarge exakt gerade ist, nützt mir die Angabe, dass ich eine Deformation von 1 Millimeter haben, noch gar nichts. Ich muss wissen, wo die Deformation ist. Mit den vom SmartScan gelieferten Scandaten kann ich farblich anzeigen lassen, in welchem Bereich die Delle oder die Beule ist und entsprechend nacharbeiten. Damit kann ich effizienter und zeitsparender an das Problem rangehen und habe dabei noch eine höhere Erfolgsgarantie.“
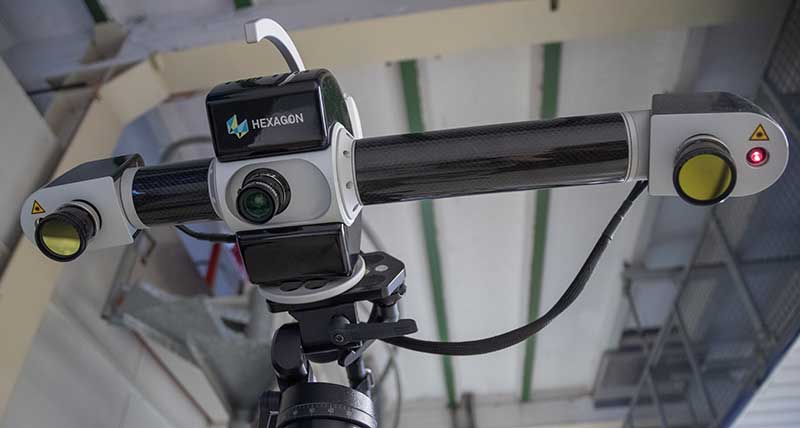
Effizient in die Zukunft
Mittlerweile ist der SmartScan voll in den Validierungsprozess integriert, wobei technische Fragen zügig vom Hexagon-Support beantwortet wurden. „Es war am Anfang ein Lernprozess, festzustellen, wie ich an die geeignetsten Maße rankomme. Aber wir haben im Laufe der Zeit alle Problemfälle, die wir hatten, gelöst. Wir sind damit sehr zufrieden“, bestätig Miguel Ramalhosa."Richtig effizient wäre es, wenn wir den Scanner auch in der laufenden Überwachung einsetzen würden", sagt Ramalhosa, der bereits über weitere Einsatzgebiete der Scan-Technologie in der Zukunft nachdenkt. In der Qualitätskontrolle der Serienfertigung kann bisher nur eine abstrahierte Checkliste mit den nötigsten Maßen überprüft werden. Eine vollständige Überprüfung wäre mit den heutigen Messmitteln zu aufwendig und zeitintensiv. Mit dem Einsatz des SmartScans an dieser Stelle könnte auch hier die vollständige Check-Liste angewendet und eine statistische Überwachung betrieben werden.